Making my Ideal Cutting, Sewing, and Crafting Table
- Kat Zimmermann
- Apr 8, 2022
- 10 min read
Updated: Jul 22, 2024

First, let me acknowledge the privilege that I currently have an entire room (floor, actually) in my house dedicated to crafting. One corner of this is my daily work-from-home space, but it's also where I edit my TikToks and write these posts so I'm counting it as part of the crafting space.
In the past, my cutting and sewing work tables have been the floor, my kitchen table, and a long folding table on a set of bed risers. I finally have the space and the money to make a cutting table that's at the right height for my 5'7" frame, has a ton of storage, and is actually large enough to cut out pattern pieces without needing to oh so carefully maneuver them over the edge of the table.
This is something I've wanted for a long time and I'm thrilled it's finally done. There are many DIY crafting tables out there that are similar, but this one is mine. Read on for step-by-step instructions on planning and building your own cutting table!
Q: What materials do I need to replicate this table? How much did it cost?
A: To make my cutting table, I used the following (non-affiliate links included):
Two IKEA KALLAX units in grey/wood effect (mine were purchased on Facebook marketplace for $100 total)
Two sets of 6 inch gold legs (total $40)
One 4 x 8 ft sheet of melamine ($44) - a Home Depot employee cut this for me so the final top is 4 x 6 ft.
--> DAD TIP: Put a strip of masking tape all the way around where it needs to be cut to prevent the melamine from chipping.
One roll of melamine iron-on edging ($15)
One white putty stick ($7.50)
One box of 1 inch drywall screws ($7.47)
One box of 1/2 inch drywall screws (I haven't purchased these yet)
6 medium sized mending plates for attaching the shelves to each other ($13.20)
4 small L-brackets for mounting the tabletop ($6.47)
14 DRÖNA boxes ($7 each --> $98 total)
TIP: If you want to buy these over time, be aware that they change the available patterns very frequently. Once it's gone, it's never coming back.
2 KALLAX inserts with drawers ($40 total)
Grand total: $371.64 (+ the screws I still need to buy)
Finding cube storage boxes secondhand is a good way to bring down the cost. Of course, you can also choose to leave the cubes open which would save you $138 from the above list.

Q: Was this difficult to build?
A: No - I don't consider myself a handy person although I am comfortable using a drill. The KALLAX units are light enough to be moved around by one person. Once attached, I was able to flip it around and over by using one corner as a fulcrum - still not super heavy, just a little awkward. I would overall say this a pretty beginner-friendly construction project. You will probably want a second person to help mount the tabletop and/or carry things up stairs if you have them.
Q: What tools do I need to put everything together?
A: To put this together, I exclusively used my handheld power drill, mainly with a phillips head bit to bit the drywall screws. I did use a hand screw and hammer to assemble the KALLAX inserts as well. A putty knife and hairdryer or heat gun are helpful for applying the putty stick.
Q: How long did it take to build the table?
A: I built this table over the course of about two weeks. Start to finish, I would estimate about 5 - 6 hours of work.
The Planning Phase

If you've not yet read my listicle on 10 things every crafter needs to hear - this is #3. Taking the time to think through not only what you want but what will be useful long term is entirely worth it. I initially drew out a basic design but made small changes and additions to the plan over the course of about a month before starting to actually do anything.
I wanted the following features:
A BIG cutting and work surface
The cutting surface shouldn't be so big that I can't easily reach the center
A surface that can be fully walked around so I can work from any side (this meant getting rid of a set of plastic drawers that I've had since probably 2008)
Storage to replace the plastic drawers but also generally extra space to squirrel things away
Height - tall enough to be comfortable working on while standing without back pain - I measured this and decided 36 inches would be about right
Durable surface that will wear for a long time
Ability to take apart and move out of this house - this one meant absolutely no glue!
One additional feature - a roll-over the top ironing mat the size of the table's surface that will store under the overhang on one side of the table. This will be a part 2 post for sure.
Research and Shopping
I don't consider myself handy, so I knew I wasn't going to build this from scratch. I started by looking at IKEA hacks because there's an IKEA store close to me and their prices are very affordable. In looking at what others have done, KALLAX seemed to be the way to go.
It's worth noting that while this is certainly not the only piece of IKEA furniture that fits the bill, it's the most affordable and readily available. If you want something with a lot of drawers, the Alex drawer units are a good option and come in several sizes. Dressers can also be an option, just be wary of height.
With respect to layout, I originally thought I would make a table similar to Bernadette Banner's with the two units at either end of the table and empty space under the table in the middle. I changed my mind for two reasons:
The countertop size required to do this was awkward - either too short or too side. Importantly, it was also not a standard size that would be easy to get.
I was concerned about structural integrity of having a long long table with no supports in the middle.
I ultimately decided that putting the units side to side running along the length of the top would offer the most support without losing easy access to the cube storage spaces. After choosing the layout, there were a few more problems I ran into:

Problem one: the KALLAX units were either too tall (3 cubes) or too short (2 cubes). I fussed about this for far too long before I realized that adding furniture legs is not difficult and could provide the extra 6 inches of height I needed. Legs also provided an opportunity to add some style to the piece and mean that I'll be able to vacuum under the table.
Note: a lot of people choose to use casters instead of legs so they can roll the table around the room. My room is carpeted so this was not an option, but casters are a great choice for non-carpeted spaces. Be sure to choose casters that lock into place and support the weight of the full unit. Add extra height with plywood sheets if needed (Morgan Donner's table build is a good example).
Problem two: my local IKEA was totally out of stock of KALLAX units in white. I'm very wary of purchasing anything from IKEA in a "unique" color as they sometimes stop making them and you can't get replacement or matching parts. I originally wanted to go with white cubes and a butcherblock top. Since the white was totally out of stock at my store and wouldn't be back in for several months, I turned to Facebook Marketplace. The great thing about living near an IKEA is that everyone has furniture from IKEA and many folks are looking to sell their pieces. Within about a month of regularly looking, I found someone selling the two matching units I needed. They weren't my preferred color, but $100 for both of them was a good deal. Buying secondhand also meant (1) the units were already assembled and (2) I wasn't purchasing anything new which is always an environmental pro.
Problem 3: choosing a topper. I spent a LOT of time looking at countertops. I considered buying two countertops and joining them together as well as buying a pre-fab island countertop. None of these were going to work because of the size restrictions and the fact that this would run me at least $300. Pass. A lot of people have used plywood but I was worried about snagging fabric on the surface, even if I put a lot of time into sanding and finishing. Shout out to my dad for reminding me that melamine exists and is super affordable - just $44 for a 4 x 8 ft sheet. A clear winner.

Assembly
General Note: If you use coarsely-threaded screws (like drywall screws), there's no need to drill pilot holes. The screws should go straight in, just put a little weight behind the drill.

(Step 1) Decide which face of the KALLAX units will be the bottom and place the units side-by-side with the bottoms facing up. Press the units as close together as possible and add the mending plates. The mending plates are placed as follows:
For this description, the cubes are numbered 1 - 8 from left to right where 1 - 4 are the top row and 5 - 8 are the bottom row. The table side is above 1 - 4 and the leg side is below 5 - 8.
Two mending plates are on the underside of the top shelf, one each at the center top of cubes 1 and 4.
Two mending plates are near the centers of the sides, one on the top of the left side of cube 5 and one at the top of the right side of cube 8
Two mending plates are on the very bottom, below cubes 6 and 7 but NOT in the cubes
If you use the diagram, remember that your units are currently upside down.
To install, start with the mending plates on the underside of the top of the unit (currently closest to the floor) and work your way up to the very bottom of the units (currently closest to the ceiling). Remember to press the units together as you affix the mending plates at each step.
QUICK CHECK: How long are your screws? 1 inch screws are fine to go around the outside of the KALLAX, but will punch all the way through the center shelves and dividers.


I may have (did) made the mistake of forgetting to read my own notes and screwing all the way through the center of the middle shelf. If you also make this mistake, here's what I did to fix it: remove the screws, sand it down to be flat, color in the wood with a grey sharpie. I didn't have any functional wood putty on hand and the holes are going to be covered with cubes at all times anyway so it's not as big a deal as it seemed at 9pm the night I discovered my error.
After adding all the mending plates, give the whole thing a wiggle to make sure it's secure.

(Step 2) Add the legs. To do this, space them out to find the arrangement you like, then screw into place. A bird's eye diagram of how I placed the legs is below. The legs I ordered did come with their own screws, but I used the drywall screws instead as they were a little more coarsely threaded. The screws don't match the gold of the legs, but it doesn't show, so it doesn't matter.


(Step 3) Flip the whole thing over so it's right side up and resting on the legs. Add any drawer inserts or cubes now, keeping in mind that drawers at the very top will be a little tricky to access after adding the tabletop. Still accessible, yes, but I recommend filling these drawers with larger things that are used less frequently.
(Step 4) Add the tabletop. At this point in time, I've not secured the counter in place with the L-brackets because I'm not 100% sure if I want it centered on the shelves. After a few projects, I'll make a decision and screw it in place with L-brackets into the sides of the unit - 2 on each side at opposite corners. Remember to use the 1 inch screws to go into the KALLAX sides but 1/2 inch screws to go into the tabletop.
(Step 5) Add the edging to the melamine tabletop. The edging I purchased did come with directions and a little bit of reading online was helpful to make sure I did this properly. To apply:

Put a piece of scrap cloth between the iron and the edging - I used a scrap rag of t-shirt fabric - be sure it's long enough to protect the entire surface of your iron.
Put the iron on the cotton heat setting with no steam. Start with a lower setting and see if it's enough to melt the glue into place. Increase the heat if needed. I found a count of 10 was about right for each section.
Start with the side of the table that will be seen the least often and begin near a corner but not at the corner (to avoid a sharp edge).
Use masking tape to hold the edging in place every foot or so as you work around the table. I taped one side length at a time and then pressed into place.
Use your fingers to lightly tug at the top and bottom of the edging after pressing into place to check it's secure. Press for an extra few seconds where needed.
Turn the corners SLOWLY. The melamine is a plastic and will melt and bend into place, but be careful not to crack and break it. I didn't need any extra tools to do this, but others have used a heat gun or hairdryer for extra targeted melting.
Use a pair of sharp scissors (NOT fabric scissors, you heathen) to cut the edging where it meets with itself after going all the way around.
(Step 6) Repair any chips along the edges. To do this, melt the tip of the putty stick using a hairdryer or heat gun and press into any chipped spots around the edges. Smooth over with a putty knife and wipe away excess with a rag. I've not yet done this step as I'm still waiting for my putty stick to arrive.
(Step 7) Fill your storage bins and revel in your success!

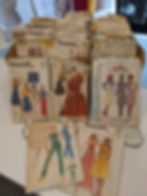
Will you make a cutting table? Will you add your own adjustments or flair? Share out in the comments below!
I'm thrilled with how my cutting table turned out - this also means I'm nearly finished with my craft room overhaul! What's left is to find a chair for the corner, finish restoring my antique sewing machine cabinet, and relocate all of our books to their new space in a different part of the house. The goal is to finish everything by the end of Summer - distant cheering and good vibes welcome 😎
Side note: I bought this giant box of vintage patterns at an estate sale and I can't decide what to sew first!
You can follow the blog by filling out the form at the bottom of the page so you never miss a post! Follow me on @craftematics on TikTok, Instagram, or Facebook for extra crafting content and to share your own content with me - I love to see what you make!